Your Guide to Selecting MQS Barn for Premier Steel Building Projects in Montana — When embarking on a project concerning steel buildings in Montana, it’s imperative to consider MQS Barn as a leading solution. Offering durability and versatility, metal buildings in Montana have surged in popularity, especially those involving steel building construction.
These structures provide unparalleled strength against Montana’s diverse weather patterns, making steel buildings a prudent investment for any commercial endeavor. Selecting the right MQS structure involves understanding the nuances of metal building construction in Montana, from supplier quality to construction expertise. Keep reading to discover how to successfully manage your steel building project from conception to completion.
- Choosing the Right MQS Barn for Your Montana Project
- Why MQS Barn is a Top Choice for Montana Steel Buildings
- Key Attributes to Look for in Steel Building Suppliers
- The Importance of Skilled Contractors for Steel Buildings
- Navigating Commercial Steel Building Manufacturers' Options
- Integrating Your MQS Barn Into a Sustainable Construction Plan
- Financial Planning for Your Steel Building Project in Montana
- Project Milestones and Timeline Management
- Ensuring Quality Control Throughout Your Build
- Frequently Asked Questions
- Conclusion
Choosing the Right MQS Barn for Your Montana Project
Embarking on a barn construction endeavor in the rugged landscapes of Montana necessitates a meticulous approach to selecting the appropriate steel building. Identifying the specific requirements of the construction project stands as the initial stride towards a successful build. A comprehensive understanding of Montana’s unique climate conditions plays a vital role in choosing a steel structure that can withstand the varying weather patterns.
Exploring the diverse models and options offered by MQS Barn allows for customization in line with the intended use and aesthetic preferences. Engaging with a local MQS representative provides invaluable insights that align with regional standards and expertise. Lastly, a coherent grasp of the project’s timeline and financial scope ensures the seamless integration of the chosen metal building, complete with a durable roof and quality manufacturing, into the envisioned agricultural or commercial landscape.
Identify Your Construction Needs
As you embark on a barn construction project in Montana, assessing the functionality requirements becomes the foremost task. Consider if the barn will harbor animals, serve as self storage, or function as a warehouse; each purpose demands unique spatial and structural features. For those raising horses, a barn designed for equine needs with ample space and robust stalls is imperative.
Montana’s heavy snowfall necessitates a building that can endure the weight and pressure of persistent snow accumulations. It is essential to consult with steel building suppliers to ensure the selected barn structure is engineered for snow load resilience. This step assures long-term durability and safety for your investment.
Understand Montana’s Climate Considerations
Montana, seated in the heart of North America, is characterized by a diverse climate that alternates between the bitter cold of winter and the warmth of the summer months. When designing barns, an environmentally friendly approach with an emphasis on suitable roof pitch and building insulation is critical to maintaining inside temperatures and minimizing the building’s impact on the natural surroundings.
High-quality insulation contributes to a barn’s energy efficiency, reducing the need for excessive heating during the freezing periods. Equally important, the right roof pitch design is not merely aesthetic; it serves a functional purpose, allowing snow to slide off easily, preventing accumulation that could compromise the structural integrity of the steel building.
Explore MQS Barn Models and Options
Within the realm of MQS Barn, one will find a diverse array of models suitable for a multiplicity of purposes, from storied carriage houses to straightforward single-story garage structures. Each model offers the convenience of prefabrication which streamlines the installation process, providing time savings and potentially lowering overall costs.
To accommodate projects across varying budgetary constraints, MQS provides a price-sensitive assortment of barn designs. Clients can opt for turnkey solutions that involve the comprehensive handling of project details from inception to completion, particularly beneficial for those in Connecticut pursuing an expedited construction schedule.
Consult With a Local MQS Representative
Engagement with a local MQS representative provides an individual, customer-centric experience, ensuring that your steel building construction meets the specific requirements of your project. These individuals possess a wealth of knowledge in selecting the most suitable barn designs for the varied Montana climate and can guide customers through a range of options that align with their construction objectives.
Moreover, collaborating with an MQS representative can greatly facilitate communication between all parties involved, including general contractors and retail suppliers, streamlining the selection process. With their expertise, customers gain access to insights that directly impact the structural efficiency and functionality of their barn, tailored to their distinct needs.
Consider the Project Timeline and Budget
Timely completion hinges on careful engineering and adherence to building codes, ensuring a smooth and efficient construction process. Selecting the right team with ample experience in steel barn projects is crucial, not only for punctuality but also to maintain cost-effectiveness throughout the build, especially when erecting specialized structures like airplane hangars.
Vetting the financial aspects of your barn construction includes evaluating engineering service fees, material expenses, and potential cost fluctuations. Transparency about costs from the outset aligns with building codes and assures an economically sound investment without compromising the structural integrity or functionality of your new barn.
Investing in the right barn transforms your Montana project. Discover why MQS Barn stand out as the premier choice for durable steel buildings.
Why MQS Barn is a Top Choice for Montana Steel Buildings
MQS Barn emerges as a well-respected company that understands the complexities of Montana’s climate, offering steel structures that champion the amalgamation of strength and aesthetic appeal. Through rigorous selection of building materials, each barndominium stands resilient against the fickle moods of Montana weather. Clients have the luxury to tailor their buildings for a variety of applications, ensuring each structure aligns with the client’s vision and purpose.
Energy efficiency is an integral aspect of MQS Barn’s design, allowing clients to conserve energy within their steel buildings. Montana residents, familiar with severe weather conditions, have recognized the durability of these energy-efficient barndominiums. This guide showcases community feedback and detailed project case studies, providing tangible insights into the company’s ability to meet and exceed construction expectations with premier building materials and customizable options.
Durable Materials Suited for Montana Weather
For a steel building to endure the strenuous demands of Montana’s climate, choice of material is paramount. MQS Barn places significant emphasis on utilizing a robust steel frame designed to resist the variable weather, ensuring projects achieve long-lasting durability that withstands harsh winters and demanding summer suns.
Project management teams at MQS Barn prioritize not only sturdy construction but also exceptional customer service, guiding Montana residents through the selection of steel structures that include resilient sheds matched to regional requirements. The commitment to client satisfaction and quality material selection positions MQS Barn as a steadfast provider in the industry.
Customization Options for Every Use
MQS Barn recognizes that no two building projects in Montana are the same, with each requiring a bespoke space to fulfill distinct needs. To address this, MQS offers a vast selection of customization options, from varying dimensions to specific architectural features, ensuring that every steel structure is tailored to the precise specifications of the client’s project.
Before finalizing the details of a custom barn, clients can access a wealth of information on the MQS website, including a detailed FAQ section and resources on how zip code may influence building requirements. This guidance is particularly beneficial for owners seeking clarity on how local regulations may impact insurance and other aspects of barn ownership.
Energy Efficiency Features
MQS Barn’s advanced steel structures offer noteworthy energy savings, bolstered by superior insulation techniques. Individuals invested in agriculture recognize how these features can significantly reduce the operational costs associated with maintaining a comfortable environment for livestock or produce storage.
Montana’s push towards eco-friendly construction practices is mirrored in the warranties provided with MQS carports and barns. These guarantees not only ensure long-term structural integrity but also promise sustained energy efficiency, meaning online searches often lead to MQS as a resource for green building options in Montana.
Community Feedback and Project Case Studies
Customer testimonials highlight the innovation inherent in MQS Barn’s approach to steel building construction in Montana. Users frequently note how the company’s cutting-edge designs and sustainable building practices lead to increased satisfaction with the completed projects.
Case studies of barns that endured the fierce Montana wind demonstrate the durability of MQS constructions, surpassing traditional wood frameworks. These reports often praise the resilient paint finishes that withstand the elements, maintaining their integrity and appearance year after year.
MQS Barn stands out as a premier provider of Montana steel structures, setting a standard in quality and durability. Now, let’s examine the essential qualities that make a steel building supplier truly exceptional.
Key Attributes to Look for in Steel Building Suppliers
Choosing the right supplier is critical when investing in steel buildings, as this choice can make a profound difference in the outcome of any Missouri barn or commercial structure. A reliable supply chain and quality materials are the bedrock of any successful construction project, serving as the essential tools needed to ensure structural integrity. Suppliers who offer comprehensive service packages can significantly aid clients in stream to cementing project plans, navigating green building trends, and meeting budget constraints.
Additionally, competitive pricing structures represent a cost-effective path to obtaining premium materials without overstretching financial resources. Quality customer support, paired with dependable after-sales service, completes the framework for a satisfying construction experience, offering peace of mind long after the concrete has set and the doors to a new steel edifice open.
Supply Chain Reliability and Material Quality
A robust supply chain is pivotal for any steel building project to progress without disruptions, particularly when sourcing materials from a factory setting. Maintaining a steady flow of quality steel, relevant fixtures, and additional components, suppliers provide a foundation of reliability that enables timely storage and construction phases, a benefit that savvy general contractors fully appreciate.
In selecting a supplier for steel buildings, the caliber of materials directly influences the standing and resilience of the end structure. Leading architects endorse suppliers that uphold stringent quality controls and source materials from reputable factories, ensuring that each steel component meets the demanding conditions of Montana’s diverse climates and landscapes.
Comprehensive Service Offerings
MQS Barn’s comprehensive service offerings cater to clients spanning multiple states, such as Montana, Idaho, and Wyoming. Facilities with accessible email addresses ensure prompt communication, enabling project updates and consultations to transition seamlessly across state lines, hence making the company’s full menu of services readily available regardless of geographic location.
In these states, where weather patterns may vary significantly, the ability to interact with the supplier’s diverse service options without extended delay is advantageous. This ensures that any modifications to the design or structure can be addressed swiftly, maintaining momentum and adherence to the project timeline, a testament to the supplier’s commitment to excellence and customer convenience.
Competitive Pricing Structures
When seeking superior steel buildings for aviation hangers or farm outbuildings in Montana, potential buyers should examine suppliers that offer competitive pricing structures. By requesting a free quote, customers can evaluate overall affordability while ensuring that essential components, such as durable metal roofing, meet their financial planning criteria.
Customers in other regions have found that suppliers with transparent pricing policies enable them to allocate funds efficiently across their building projects. These competitive prices ensure that farm owners and aviation enthusiasts receive value while investing in robust structures designed to endure the unique climatic challenges Montana presents.
Customer Support and After-Sales Service
Customer support emerges as a cornerstone in the partnership between steel frame contractors and their clients. Throughout the Northwestern States, the demand for skillful representatives who can provide guidance on the installation of a metal roof or the construction of a full steel frame property is considerable.
After-sales service is equally vital, ensuring the longevity and satisfaction with each project. Quality after-sales assistance provides property owners with the assurance that any post-installation concerns related to their metal roof or structural integrity will be managed promptly and professionally.
Selecting a reputable steel building supplier is only the first step. Now, let’s consider the pivotal role of skilled contractors in the successful construction of steel buildings.
The Importance of Skilled Contractors for Steel Buildings
The success of steel building projects, particularly those involving the intricate details of sheet metal and framing, hinges substantially on the abilities of the contracted builders. In Montana, professionals must hold credentials and certifications that assure competence with the state’s specific construction demands. Their portfolio, reflecting completed projects in Montana, Wyoming, and Idaho, often serves as proof of their capability to execute complex building tasks.
Moreover, a deep understanding of Montana’s building codes is non-negotiable, ensuring each project abides by regional regulations. Effective contractors possess advanced communication skills, allowing them to convey critical information via text messaging or other means to maintain project transparency. Their project management capabilities are equally crucial, orchestrating the myriad moving pieces of construction to deliver a final edifice that satisfies all stakeholder expectations.
Credentials and Certifications Specific to Montana
Contractors in Montana seeking to construct prefabricated buildings, such as those provided by MQS Barn, must have certifications indicating their proficiency with building systems. Such qualifications ensure that each construct, whether clad in stucco or designed for the ease of truck access, is completed to the highest standards of quality and safety.
It is a pleasure for clients to work with Montana contractors who are well-versed in the nuances of prefabricated building systems, including those utilizing steel. Recognition of these certifications assures that the structures will be erected accurately, efficiently, and in accordance with local building codes.
Portfolio of Completed Projects in the Region
A contractor’s portfolio, brimming with successfully accomplished steel building initiatives across multiple states, acts as tangible testament to their expertise. Such a repository of work, showcasing both versatility and a keen understanding of different climatic and structural demands, instills confidence in their ability to deliver a stable and durable edifice.
In a field teeming with competition, a brand that presents a substantial catalog of completed projects across varied regions, including the challenging terrains of Montana, positions itself as a leader in the market. Displaying competency through varied architectural feats, these projects affirm the brand’s commitment to excellence and client satisfaction.
Understanding of Local Building Codes
When selecting contractors for steel building projects in Montana, placing attention on their knowledge of local building codes is crucial. Stringent regulations require builders to maintain a heightened awareness of area-specific standards, a critical factor that contributes to achieving customer satisfaction.
Contractors with comprehensive understanding of Montana’s building codes deserve credit for the smooth approval and durability of the steel structures they erect. Their expertise ensures seamless compliance, securing the integrity of the building projects, and ultimately reinforcing the trust of their clients.
Communication Skills and Project Management Capabilities
Effective communication stands as a linchpin of successful project management in the construction of steel buildings. Contractors proficient in conveying project intricacies enable a streamlined workflow, critical when coordinating tasks. Such communication prowess ensures that all stakeholders remain informed and cohesive throughout the project’s lifespan.
Project management, an integral component of steel building construction, demands robust abilities to orchestrate the complex facets of a build. Skilled managers adept in this realm lead projects to fruition with finesse, no matter the weather conditions. Mastery in management translates to projects completed on schedule and within budget, reflecting proficiency in leading diverse teams and resources.
Choosing a skilled contractor for your steel building is just the first step. Next, let’s navigate the myriad of manufacturers to find the perfect fit for your commercial barn construction needs.
Navigating Commercial Steel Building Manufacturers’ Options
When venturing into the arena of commercial steel building projects, the decision to collaborate with a reputable manufacturer is not one to be taken lightly. A manufacturer’s reputation in the industry acts as a beacon for potential clients, signaling a history of quality and reliability. Specifically, businesses from as far afield as Arkansas and Alabama observe the accumulated feedback and success stories to gauge whether a similar investment will yield anticipated benefits in Montana.
Warranty and guarantee terms are also pivotal, offering assurance against future issues with the structure post-erection. With logistical efficiency paramount, the manufacturer’s proximity to the site influences not only shipping costs but also impacts the carbon footprint of the project. Additionally, the availability of custom design services enables a tailored approach that meets the unique needs of each project, reinforced by the convenience of SMS updates throughout the design and construction phases.
Assessing Manufacturer’s Industry Reputation
In the expansive domain of commercial steel buildings, discerning the reputation of a manufacturer is a foundational step. Clients in Montana, Idaho, and Wyoming, for instance, use past performance, client testimonials, and completed agriculture and commercial steel projects, like wineries or processing plants, as indicators of a manufacturer’s credibility and capability.
Considering a company’s reputation becomes paramount when specialized builds, such as a plant in Montana or a winery in the heart of Wyoming, are involved. The right manufacturer will have a track record of delivering quality buildings on time and within budget, critical elements for long-term success and client satisfaction.
Warranty and Guarantee Considerations
When choosing a steel building, especially one that may house aircraft or other significant assets, warranty and guarantee offerings are a testament to a manufacturer’s confidence in their product. These assurances safeguard the aesthetic integrity and structural soundness over a given span, providing peace of mind well beyond the point of sale.
The duration and breadth of warranties can greatly influence the upkeep and longevity of steel structures. A robust warranty not only covers the basics but extends to details such as the paint finish and roof integrity, ensuring that every square foot of the building remains protected against the elements.
Proximity to Montana and Logistic Efficiency
In the arena of commercial steel building fabrication, the proximity of the manufacturer to the Montana area significantly streamlines the entire process. Hiring experts from nearby maximizes logistic efficiency, reducing delays in the supply of pivotal components such as welding materials, trusses, and other construction essentials.
Moreover, a manufacturer with facilities close to the project site can respond swiftly to onsite demands, ensuring that experts are available to address any truss or welding challenges promptly. This logistical advantage can also favorably impact a project’s credit score by minimizing unexpected costs and maintaining timely completion schedules.
Availability of Custom Design Services
The bespoke design services offered by steel manufacturers cater to an array of trade requirements, seamlessly integrating buildings into the Iowa landscape. Businesses aiming to establish a state-of-the-art distribution center will find custom design services invaluable for meeting specific operational needs.
Whether a company seeks an expansive space for product storage or a strategically located broker office, customization allows the structure to align with the unique demands of commerce and trade. This tailored approach ensures that every construction not only enhances efficiency but also complements the surrounding Iowa landscape aesthetically.
Transitioning from choosing a manufacturer to actual construction raises the stakes. Now, let’s seamlessly move into crafting a sustainable plan that ensures your MQS barn stands the test of time.
Integrating Your MQS Barn Into a Sustainable Construction Plan
Embracing a sustainable approach when developing an MQS barn positions the structure as a cutting-edge addition to Montana‘s architectural sphere, serving as more than just a basic workshop or storage facility. It may be a source of pride for Kentuckians eager to incorporate solar panels, harnessing the state’s ample sunshine to reduce energy costs and enhance efficiency.
Furthermore, the integration of top-grade insulation and energy-saving features into the design of an MQS Barn contributes to a significant decrease in the thermal footprint, aligning with proactive education on sustainable practices. The possibility of outfitting the building with a rainwater collection system exemplifies a harmonious bond with the environment, maximizing resource conservation.
Together with thoughtful landscaping, these eco-conscious elements transform the MQS barn into a paragon of environmentally responsible construction, resonating with a commitment to preserving the surrounding natural beauty of Montana’s diverse landscapes.
Solar Panel Installation Possibilities
Integrating solar panels into the design of an MQS Barn enhances its sustainability, tapping into Montana’s potential for solar energy collection. This addition not only aligns with recycling goals by reducing waste through renewable energy use but also demonstrates a commitment to eco-friendly building practices. Such solar energy systems are beneficial, especially in areas like Denver where solar potential is high, optimizing the energy logistics for the entire building operation.
When considering the integration of sustainable technologies into Montana steel structures, San Antonio’s advancements in the solar market can serve as a blueprint for successful installation and use. The logistics of incorporating solar panels require meticulous planning to ensure that the positioning and angle maximize sunlight absorption, contributing to a building’s overall energy efficiency and cost-effectiveness.
Insulation and Energy Efficient Features
Insulation is a crucial consideration in steel building construction for maintaining temperature control and minimizing energy loss. In locations like Wyoming and Utah, where conditions can range from sub-zero winters to scorching summer heat, advanced insulation techniques provide significant cost savings on heating and cooling. Data from recent builds in these states highlight how well-insulated MQS barn structures contribute to year-round comfort and efficiency.
Similarly, in Indiana and Montana, adopting energy-efficient features has proven to transform steel buildings into models of sustainability. This includes everything from properly sealed doors and windows to the installation of energy-efficient lighting systems and appliances. Through careful selection of such features, building owners in these regions report a marked reduction in their energy consumption, as supported by collected data.
Rainwater Collection Systems Compatibility
Strategically incorporating rainwater harvesting systems into the design of steel structures is a forward-thinking move that metal roofing suppliers are increasingly supporting. With the correct implementation, metal building supply can extend beyond structural components to include integrated water collection features that align with eco-conscious building principles.
In selecting materials for rainwater collection, it is essential to engage with steel roofing suppliers who understand the criticality of compatible sheet metal supplies. These suppliers contribute to sustainable steel building supply solutions that facilitate the collection and reuse of rainwater, embodying robust environmental stewardship.
Landscaping and Environmentally Friendly Surroundings
Incorporating landscaping that complements the natural features of the surroundings is not only aesthetically pleasing but also enhances the ecological harmony around a steel building. Working closely with metal roofing dealers ensures that choices made in the selection of roof panels contribute positively to the overall environmental sustainability of the project.
Choosing the right metal roof panel suppliers and metal roof wholesalers is crucial in supporting a sustainable construction plan that emphasizes reducing energy consumption and promoting biodiversity. Now that you have a vision for integrating sustainable features into your barn, it’s time to consider the financial aspect. Let’s explore how to budget effectively for a steel building project in Montana.
Financial Planning for Your Steel Building Project in Montana
Sound financial planning is a linchpin of success for any steel building project in Montana, where the collaboration with experienced contractors for steel buildings ensures a comprehensive grasp of the Total Cost of Ownership. Property owners aiming to erect lasting structures often engage metal building builders known for their transparency in pricing and cost assessment.
Metal building installers play a key role in this equation, assisting clients in understanding the array of financing pathways available, including potential grants that may ease upfront investment burdens. As part of the planning process, steel building builders, alongside a steel building general contractor, can help anticipate unexpected costs, fortifying the project’s budgetary framework.
By assessing the projected long-term savings and calculating return on investment estimates, owners can foresee the financial landscape of their project, ensuring a robust and informed economic strategy underpins their construction plans.
Understanding the Total Cost of Ownership
The Total Cost of Ownership for steel structures goes beyond the initial price tag. Engaging contractors for metal buildings who offer a comprehensive breakdown of all expenses involved—from material costs to labor rates—helps property owners anticipate the full financial impact of their building projects.
Commercial steel builders and steel buildings erectors must account for both direct and indirect costs in their estimates to provide clients with a realistic outlook on investment needs. Metal building contractors and metal buildings erectors are instrumental in outlining potential long-term maintenance and operational expenses for a full financial picture.
Exploring Financing Options and Grants
Montana’s steel building contractors frequently highlight the availability of financing options that can alleviate the initial financial strain of construction projects. With tailored loan programs, clients can spread the cost of their steel buildings over time, allowing greater flexibility in budget allocation.
Additionally, some clients may qualify for grants provided by governmental or agricultural organizations designed to support rural development or technological innovation in farming practices. Steel building contractors often assist in identifying and applying for these financial opportunities.
Budgeting for Unexpected Costs
Careful allocation for unforeseen expenditures is crucial to safeguarding your steel building project against potential financial setbacks. Contractors with an intimate knowledge of Montana’s terrain and construction climate advise on maintaining a reserve fund, which serves as a financial buffer against unexpected variables that may arise, such as increased labor costs or price surges in raw materials.
In the planning phase, a thorough risk assessment carried out by seasoned Montana barn constructors can pinpoint possible financial risks inherent in steel building projects. They can assist property owners in earmarking a portion of the budget to address these risks, ensuring the project’s financial health is secure throughout its duration.
Long-Term Savings and ROI Estimates
Calculating the return on investment (ROI) for Montana-based steel buildings, such as those engineered by MQS Barn, involves analyzing long-term operational savings against initial construction costs. These savings emerge from a combination of reduced maintenance requirements, energy efficiency gains, and potential increases in property value due to the presence of a high-quality structure.
Montana property owners should factor in energy efficiency standards adopted by MQS Barn which contribute to diminished utility outlays over time. An outstanding ROI is often achieved through features that lower overheads, such as durable building materials and insulated panels, leading to a decrease in both heating and cooling expenses.
With financial plans firmly in place, the next step beckons: charting the course for your barn’s construction. Setting project milestones and managing the timeline are the pillars that will uphold your project’s success.
Project Milestones and Timeline Management
Embarking on a steel building project with MQS Barn in Montana requires meticulous planning to ensure timely progress through each development phase. Properly navigating pre-construction considerations, including the acquisition of all necessary permits, lays a solid foundation for a smooth build. Project managers must deftly guide construction through its key phases, from laying the groundwork to erecting the structure.
Proactive management of delays and challenges, whether due to weather or supply chain disruptions, is critical to maintain forward momentum. As the build reaches completion, attention turns to compiling post-construction documentation, a step that secures the operational ready status of the new steel edifice. Therefore, a strategic approach to milestones and timeline oversight is vital for the success of your premier steel building venture in the Treasure State.
Pre-Construction Considerations and Permits
A critical step in the preliminary stage of any barn construction project involves securing the necessary permits from local Montana authorities. These permissions ensure the building complies with zoning laws, building codes, and safety regulations, setting the stage for a lawful and secure construction process.
Experienced MQS Barn project managers work closely with clients to navigate the complex permitting landscape. This proactive approach prevents costly delays and ensures that every aspect of the Montana steel building project adheres to recognized standards from the outset.
Key Phases in the Construction Process
The construction process unfolds in distinct, deliberate stages, each aiming for precision and adherence to the outlined project specifications. An initial phase, site preparation, involves clearing, grading, and stabilizing the land to ensure a suitable foundation for the barn structure. Following site readiness, concrete foundations are poured, anchoring the frame securely to the ground, an unequivocal prerequisite for the subsequent erection of the steel framework.
Once the foundation sets, assembly of the prefabricated steel elements commences. This phase calls for skilled craftsmanship as each beam, column, and panel is methodically positioned, interlocked, and secured. Throughout this critical stage, stringent quality checks are imperative to confirm that each installation aligns perfectly, ensuring the integrity and safety of the completed steel building.
Managing Delays and Challenges
Contingency planning is a fundamental aspect of project management that anticipates potential obstacles during the construction of an MQS Barn structure. Project leads must be adept at devising strategic responses to unforeseen events such as material delays or labor shortages, ensuring project resilience against all odds.
The efficacy of responding to such disruptions rests on clear, proactive communication between the construction team, suppliers, and the client, aimed at minimizing any negative impact on the project timeline. In the event of an unanticipated hold-up, a swift and informed response is crucial in preserving the progression and eventual success of the steel building project.
Project Completion and Post-Construction Documentation
Upon the culmination of a barn construction project, the final inspection and approval from Montana’s building authorities are indispensable steps, marking the endeavor’s successful completion. This crucial process confirms compliance with all the standards prescribed by regulatory entities, signifying that the newly erected MQS Barn meets safety, design, and functionality benchmarks.
After securing official approvals, the compilation of comprehensive post-construction documentation is undertaken. This critical record includes warranties, maintenance guidelines, and detailed blueprints, providing owners with an essential reference that ensures informed management and upkeep of their new steel building.
As your barn begins to take shape, meticulous attention to detail is vital. Let’s discuss how consistent quality control can safeguard the integrity of your construction project.
Ensuring Quality Control Throughout Your Build
Meticulous attention to quality control is imperative when undertaking a steel building project with MQS Barn in Montana. From the outset, builders must prioritize the procurement of high-quality materials, ensuring the durability and safety of the structure. Regular inspections and compliance checks form the backbone of the construction phase, validating that every element of the build meets or exceeds regulatory standards.
Collaborating with trusted suppliers and contractors underscores a commitment to excellence and reinforces the integrity of the build. Culminating the project is the final review and handover process, a thorough evaluation that certifies the precision and quality of the finished edifice before its official turnover to the client.
Selection of High-Quality Materials
The foundation of any durable MQS Barn in Montana starts with the judicious choice of building materials. Quality steel fortified with the appropriate grade and tensile strength invites longevity and resilience, crucial attributes for structures poised to endure Montana’s dynamic weather patterns.
Selecting materials that are both robust and compliant with the latest construction standards is non-negotiable. It ensures that the barn not only stands the test of time but also adheres to safety regulations, bolstering the confidence of those investing in these functional edifices.
Regular Inspections and Compliance Checks
In the construction of MQS Barn, consistent oversight is crucial to safeguard adherence to specifications and regulations. Regular site visits by certified inspectors ensure that each phase of the build, from the structural framework to the final finishes, aligns precisely with governing codes and the high-quality standards expected of premier steel buildings.
Compliance checks are integral to the process, involving rigorous assessments by third-party entities to verify that construction methodologies, material applications, and safety protocols are in strict conformity with all relevant building regulations in Montana. This level of scrutiny is essential to uphold the structural integrity and credibility of MQS Barn constructions.
Working With Trusted Suppliers and Contractors
Partnering with reputable suppliers and contractors is a critical component of fostering a high-quality steel building project in Montana. These professionals bring a level of expertise and experience, crucial for navigating the specific requirements of robust barn construction and ensuring the use of materials and practices that align with the project’s stringent quality demands.
The successful outcome of a steel building project hinges on the collaborative efforts of contractors and suppliers who are committed to excellence. Their proficiency ensures that the construction process progresses smoothly, adhering to the project’s timeline and quality standards without compromising on the integrity or safety of the structure.
Final Review and Handover Process
The final review is an integral phase in the barn construction process, marking the occasion when every meticulous detail of the build is assessed. This thorough examination, led by the project’s quality control team, aims to ensure the final product adheres to all the outlined specifications and exudes the standards of excellence that MQS Barn represents.
Upon passing the final review, the handover process commences, transferring stewardship of the newly constructed steel building to the client. During this stage, any necessary operational training is provided, keys are exchanged, and the conclusive paperwork, ensuring a full transfer of responsibility, is executed with precision.
Frequently Asked Questions
How do I choose the right MQS Barn for my project in Montana?
Selecting the suitable barn for your project in Montana involves evaluating your specific needs, such as the intended use, size, and style preferences. It’s important to consult with professionals experienced with the local climate and building codes to ensure a functional and compliant structure.
What makes MQS Barn suitable for Montana’s climate?
MQS Barn designs structures with robust materials that withstand Montana’s fluctuating temperatures and heavy snowfall. Their structures include features that ensure ample insulation and ventilation, crucial for the state’s diverse weather conditions.
What should I look for in a steel building supplier?
When selecting a steel building supplier for barn construction, focus on their reputation for quality and reliability. It’s important to ensure they offer detailed customization options to suit your specific needs.
Why is hiring skilled contractors important for barn construction?
Hiring skilled contractors for barn construction is vital because they possess the knowledge and expertise required to ensure the structure is safe, secure, and meets all regulations. Their experience helps guarantee the durability and functionality of the barn, addressing specific needs such as animal housing or storage requirements.
How can I integrate sustainability into my barn construction?
Integrating sustainability into barn construction often involves using renewable materials and implementing energy-efficient designs. Strategies such as installing solar panels and utilizing rainwater harvesting systems can significantly reduce a barn’s environmental footprint.
Conclusion
Selecting the right MQS Barn ensures Montana steel building projects meet specific needs while withstanding the state’s variable climate. Through careful consideration of materials, design, and construction methods, these structures offer longevity, functionality, and energy efficiency.
Knowledgeable local MQS representatives guide clients through the process, ensuring compliance with regional codes and maximizing customization options. Ultimately, MQS Barn represents a wise investment, poised to fulfill commercial demands and align with sustainable building practices in Montana.
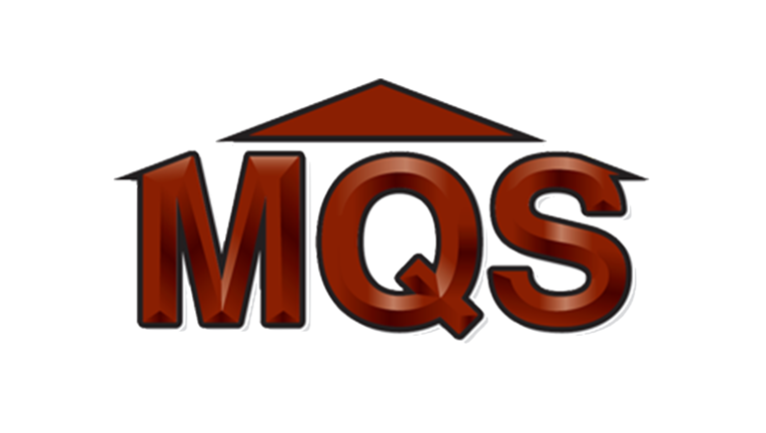
MQS Barn – Metal Buildings in Montana
We have you covered if you want new post frame agricultural buildings in Montana. When you are ready to start, our team of custom post-frame builders can work with you to ensure you get the building you need.
MQS is a family-owned and operated company specializing in post-frame, steel-sided structures, and custom pole barns in Montana. The co-founder and co-owner of MQS Barn, Mark Stoltzfus, began his building career with his Amish Mennonite family and applies the same work ethic and expert craftsmanship on every project we do in Montana.
Call us today at 855-677-2276, or contact us online to receive a free quote on your next post frame building in Montana. We look forward to hearing from you soon!